Engineering at Metalliferous Mines
For the metalliferous mining sector, North Queensland remains an ideal location for further mineral discoveries and is currently Australia’s largest producer of zinc, lead and silver. The region also ranks highly for copper, bauxite and gold. Other important minerals mined in Queensland are cobalt, nickel, phosphate rock, magnesite, magnetite, molybdenum, rhenium, scandium and tin. Minerals are extracted and recovered through underground and open cut mining operations and processed using onsite processing plants.
Orana Engineering has been engaged by a range of metalliferous mining clients throughout Queensland, with engineering experience in the mining, processing and storage of lead, silver, zinc, gold and copper. Our clients value our industry knowledge and experience, as well as our practical North Queensland location, allowing our team to be reactive and offer local, hands-on support. We understand the importance of compliance within the metalliferous industry, with our staff keeping up to date with all relevant legislation including the Mining and Quarrying Safety and Health Act and Regulations. Further information on the Act and Regulations can be found below.
Mining and Quarrying Safety and Health Act 1999
Mining and Quarrying Safety and Health Regulation 2017
We are well equipped to offer mechanical, electrical, structural and control systems engineering services for the metalliferous mining industry, assisting with engineering for fixed plant, processing plants, conveyor belts, concentrators and site infrastructure. Explore the case studies below to learn more about the value we have added for our metalliferous mining clients.
Orana Engineering Metalliferous Mine Engineering
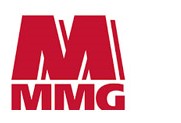
F100 Reagent Modifications
Orana Engineering was engaged by MMG's Century Mine to review a proposed reagent dosing system within the concentrator.
An investigation was conducted which included hydraulic modelling for various reagent dosing system philosophies. Results were presented for a range of design and operating conditions and three solutions were proposed meeting the client's requirements. Factoring in control system complexity and cost, Orana Engineering recommended a preferred option and a back-up option requiring only minor system modifications.
The engineering review was completed within a short timeframe and a detailed report provided to MMG detailing hydraulic modelling results and required operational settings for the offered options. MMG was able to use the results to make a decision on the solution ultimately implemented.
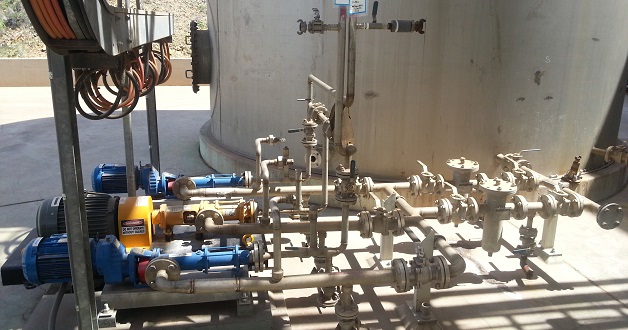
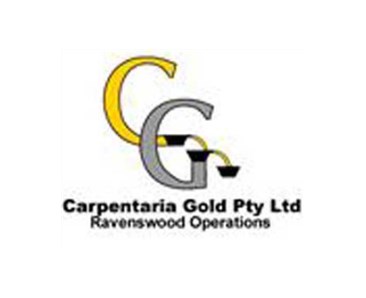
Cyanide Tank Upgrade
Carpentaria Gold identified that bunding around their Ravenswood cyanide storage tank was inadequate. Sodium Cyanide, used in the gold recovery process, is potentially lethal to humans and animals and detrimental to the environment. It is necessary to ensure it can be safely contained in an emergency.
Orana Engineering provided an innovative solution comprising a smaller tank fitted inside the existing tank. The design minimised loss of storage capacity by providing a smaller tank for primary storage whilst maintaining the existing external tank to act as the bund.
Utilising the existing tank as a bund, Orana Engineering delivered a design that met the client brief while re-using the majority of major tie-in points and providing improved access for maintenance.
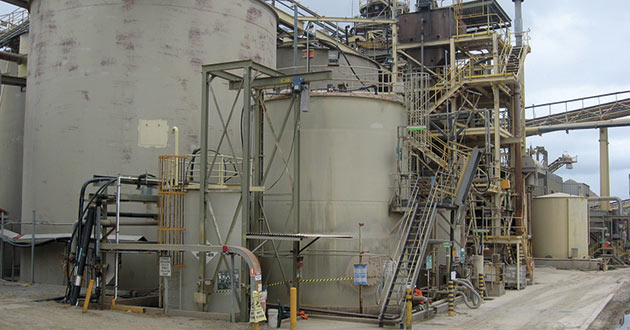
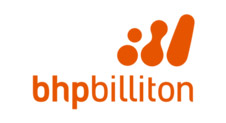
SAG Mill Cover
BHP Billiton Cannington Mine, is a significant miner and exporter of silver and lead concentrate. Orana Engineering was engaged to provide workshop fabrication drawings for a replacement cover to address corrosion issues around flanges and access openings on the existing SAG mill trommel sump cover.
Following a site visit to obtain measurements, photos, drawings and documentation, the Orana Engineering design drafting team created a detailed 3D model of the existing structure incorporating new components to produce a set of detailed shop fabrication drawings, while also revising multiple existing drawings. These drawings were reissued for construction after receiving client approval.
The new cover sections and access panels improved the safety of trommel operation while also reducing inspection and maintenance time.
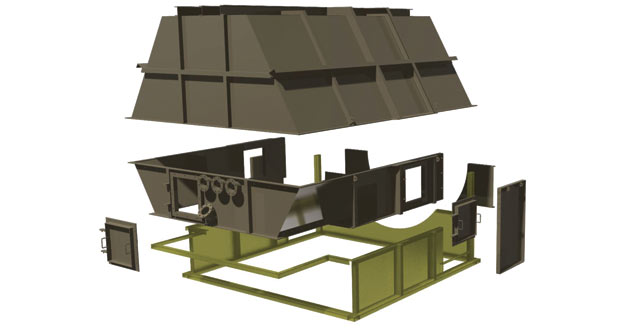
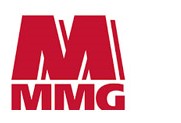
Inner Bypass Valves
Orana Engineering was engaged by MMG's Century Mine to design an upgrade within the concentrator for increased flow from a flotation cell to a tailings trough.
Orana Engineering conducted a concept investigation of available options to increase the flow rate. Results were presented for a range of design and operating conditions, and a preferred option was selected for detailed design.
Orana Engineering design staff created a 3D model of the new pipeline using Autodesk Inventor. The 3D model was used to produce fabrication drawings for pipe supports, new platform and new pipe bridge. Drawings also included isometric pipe spool drawings and revised P&ID drawings.
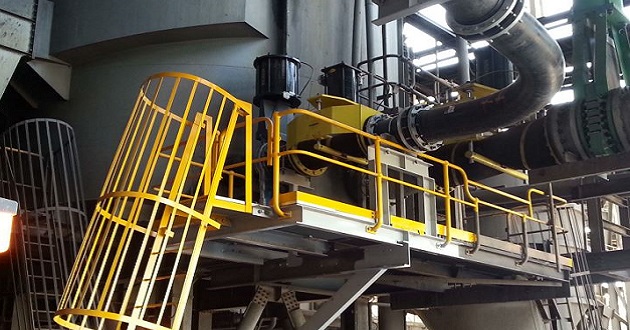
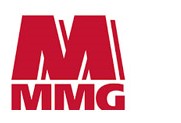
Heavy Vehicle Washdown Facility
MMG's Karumba Port Facility engaged Orana Engineering to design a heavy vehicle washdown facility to assist with management of concentrate for site vehicles and machinery. The time frame was short due to operational requirements, such that Orana Engineering worked from concept to IFC drawings in just seven days.
The design needed to accommodate a number of different vehicles from fully laden container trailers to a 30 tonne forklift, whilst also ensuring ease of facility maintenance and capture of runoff for environmental compliance.
Concept sketches were prepared, from which a detailed design was developed to meet client requirements. Through effective communication with the client Orana Engineering was able to deliver the design in a compressed timeline, to specification and budget.
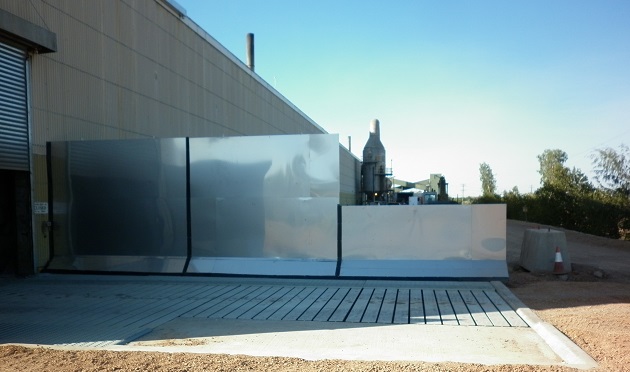
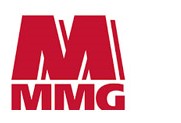
FB-028 Tank Lifting Beam
During an upgrade to the concentrator at MMG’s Century Mine, Orana Engineering was engaged to design a lifting beam for installation of a new flotation cell. The lifting beam design was to provide adaptation between lifting points on the tank and the crane, providing stability during lifting and protecting the integrity of the tank.
Structural considerations involved hand calculations and modelling in SPACE GASS based on client requirements and relevant Australian Standards. Orana Engineering's design utilised available structural members on site, providing cost benefits to the client.
Orana Engineering design staff created a 3D model in Autodesk Inventor, producing a fabrication drawing for the beam which also detailed the sling configuration for use during the lifting process.
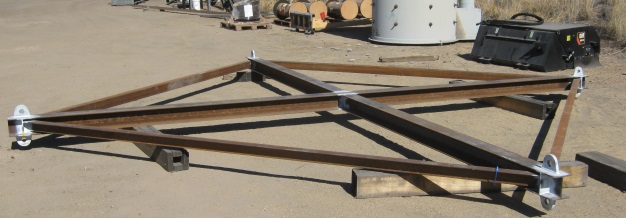
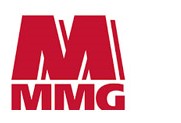
Mill Gear Box Frame
The IMT project team at MMG’s Century Zinc operations enlisted the assistance of Orana Engineering to produce a set of fabrication drawings for an existing gear box frame that required replacing. The frame had been in operation for some time, however there were no detailed drawings available for construction of a replacement unit.
The design staff at Orana Engineering created a detailed 3D model using client-supplied photos and sketches, enabling designers to produce 2D fabrication drawings for approval. A review of the drawings was conducted by the client to confirm the layout and accurate alignment with the existing installation on site. Following minor adjustments, As-Built status drawings were reissued to the client, accurately capturing detail of the existing frame.
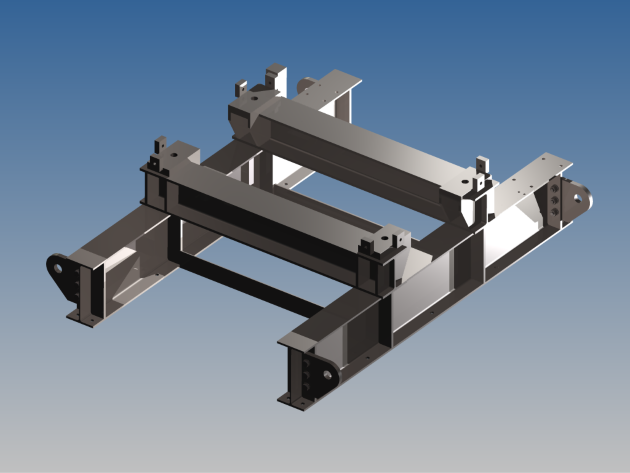
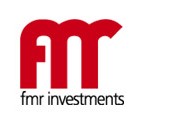
Ball Mill No. 2 Recommissioning
Eloise Copper Mine required recommissioning of their No.2 Ball Mill. During recommissioning it was identified that a means of relocating grinding media to the feed chute needed to be designed and engineered, with RPEQ certification. Orana Engineering was contacted to assist and a monorail, complete with electric hoist and trolley, was identified as being the practical solution.
Challenges presented themselves while locating the monorail within the existing structure, however Orana Engineering was able work within the constraints of the existing structure to meet client requirements. All elements of the structural engineering review and design of the monorail to were taken into account.
RPEQ certified fabrication and installation drawings were produced, ensuring the upgraded structure was fit for purpose.
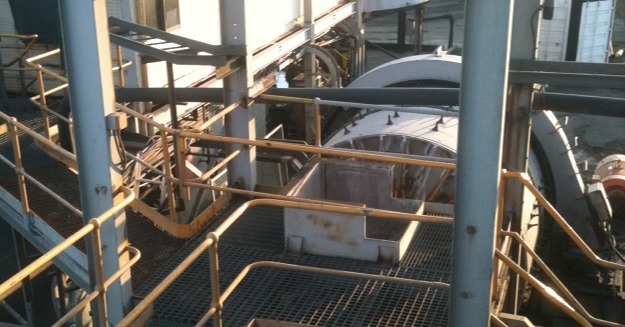
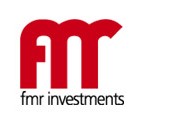
Jaw Crusher Platform
The maintenance department of Eloise Copper Mine contacted Orana Engineering with a requirement for design of an access platform for their jaw crusher, including engineering certification and drafting. The client provided site measurements and a basic concept of the design they were looking for.
Being a brownfield engineering project, the design had to consider the surrounding area and existing structures to minimise modifications. Autodesk Inventor was used to create a basic 3D model of the area. Once the physical data was established the detailed design of the platform was able to be performed efficiently.
Orana Engineering was able to produce both detailed shop drawings for fabrication and site installation drawings, all of which were provided with structural engineering certification.
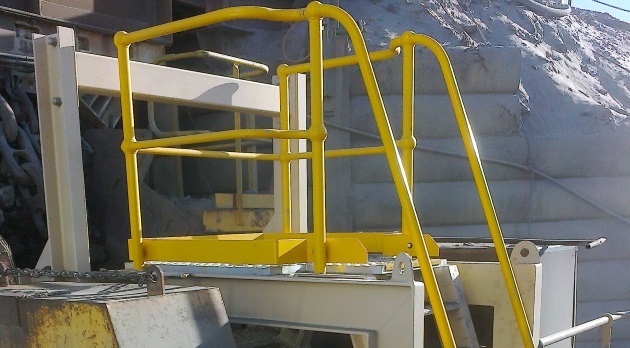
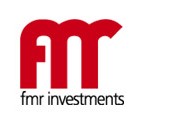
Flotation Cell Upgrade
To increase the efficiency of their concentrator, Eloise Copper Mine enlisted Orana Engineering to provide engineering and design assistance with installation of three copper concentrate scavenger cells within the existing plant.
3D models created by Orana Engineering designers were used to visually communicate solutions for new and existing equipment locations and structure arrangements. Detailing of these concept models enabled Orana Engineering to identify key tie-in locations within the plant for survey during the detailed design phase.
A multidisciplinary approach during detailed design ensured improved efficiency, with brownfield engineering challenges in relocating / connecting to existing equipment successfully achieved. Upon design completion the client was provided with an installation drawing set and scope of work.
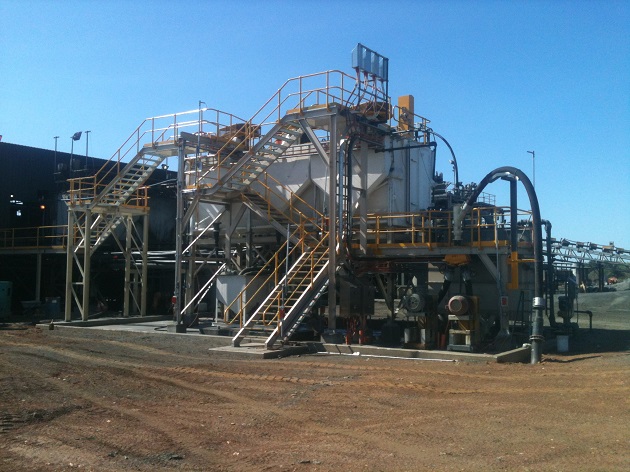